Material Models Blog Posts
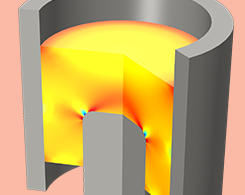
Simulating Powder Compaction with Porous Plasticity Models
Powder compaction is an important and popular technique in many manufacturing industries. You can use porous plasticity models to analyze and improve the powder compaction process.

Introduction to Modeling Stress Linearization in COMSOL Multiphysics®
Your complete introduction to the theory and process for modeling stress linearization in COMSOL Multiphysics®, as well as an overview of common real-world uses for this phenomenon.
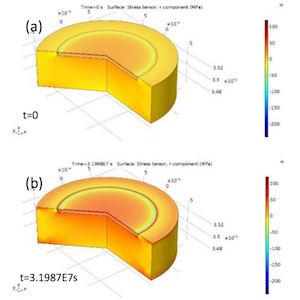
Studying the Influence of Concrete Phenomena on Sensor Performance
Some concrete structures use embedded sensors to monitor their stability, but the concrete itself can interfere with the sensors’ performance. Researchers used simulation to address this issue.
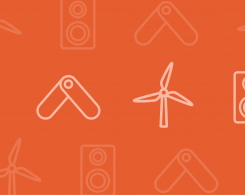
Can a Stiffness Be Negative?
Have you ever encountered an FEM formulation where the force does not monotonically increase with displacement? We discuss some examples of this behavior: negative stiffness.
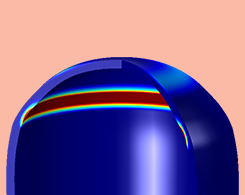
Modeling Fatigue Failure in Elastoplastic Materials
One example of fatigue failure? Bending a metal paper clip back and forth until it eventually breaks. Learn how to model this type of behavior in elastoplastic materials using COMSOL Multiphysics®.
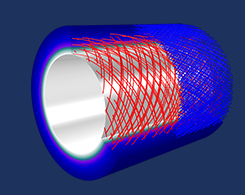
How to Model Large-Strain Viscoelasticity in COMSOL Multiphysics®
Learn how to model large-strain viscoelastic deformation, a common behavior exhibited by polymers and biological tissues, in COMSOL Multiphysics®.
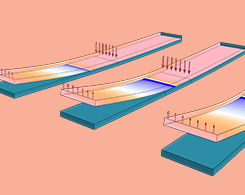
How to Model Adhesion and Decohesion in COMSOL Multiphysics
Did you know you can simulate objects that stick together once they come in contact (adhesion) as well as those that pull apart (decohesion), including full cohesive-zone modeling?

App: Analyze the Design of a Viscoelastic Structural Damper
You can use a simulation app to analyze the design and stability of a viscoelastic structural damper. Learn more in this blog post that explores a demo app you can use for inspiration.