Blog Posts Tagged Rotordynamics Module
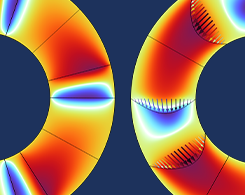
Shape and Topology Optimization of Step Thrust Bearings
Step thrust bearings support axial loads in rotating machinery. Learn how to maximize the load capacity of these bearings with shape and topology optimization.
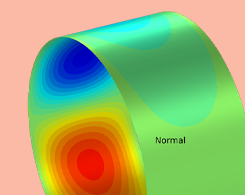
Analyzing Vibrations in Rotating Machinery Due to Bearing Misalignment
You can use structural analysis to compare the angular velocity, axial displacement, and bearing reaction moment on the shaft for rotating machinery with aligned and misaligned bearings.

Evaluating the Impact of Bearing Misalignment on Rotor Vibration
Bearings are found in devices ranging from MEMS and turbines to electric motors and even ships. How we account for a bearing’s misalignment (and the resulting rotor vibration) depends on its use.
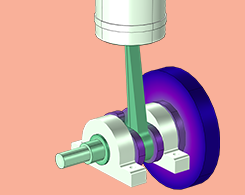
How to Model Fluid Friction in Joints with COMSOL Multiphysics®
Follow along as we demonstrate how to model fluid friction in joints using 2 rotordynamics examples: a piston and a reciprocating engine.

Predicting the Stability of Rotor Systems with the COMSOL® Software
Instability in a rotor system can lead to catastrophic failure. Fortunately, engineers can predict the stability of rotor systems by performing stability analyses with the Rotordynamics Module.

Evaluating a Turbocharger Design with Rotordynamics Analysis
Like a “turbocharged” cup of coffee, an actual turbocharger also increases speed, but in the operation of a combustion engine, not how fast your morning cup wakes you up.
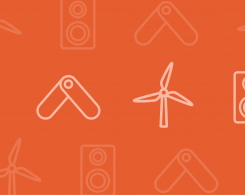
How to Model Roller Bearings in COMSOL Multiphysics®
Roller bearings are one of the most commonly used industrial components, found in gearboxes, conveyors, motors, and rolling mills, among other devices. Learn how to model this part in COMSOL®.
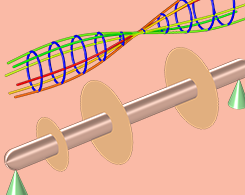
How to Perform Various Rotor Analyses in the COMSOL® Software
Check out all of the different types of rotor analyses you can perform using the specialized features in the Rotordynamics Module, an add-on to COMSOL Multiphysics®.