CFD modeling of a commercial CVD system and simulation of a CVD deposition process
Seco Tools produces inserts for machining metals. Roughly half the number of inserts Seco Tools produces are coated by Chemical Vapour Deposition (CVD) which extends the inserts lifetime in machining operations significantly. More than 10 000 inserts are coated on trays in each CVD run. A standard experimental test run in a CVD system has a relatively high cost taking all factors into account (electricity, gases, personnel etc.). It is always of interest to decrease the variation in thickness and crystal orientation of the coatings that are produced in the CVD system. Especially the thickness of the CVD coating is affected by multiple factors such as gas flows, gas temperatures and depletion of gas species. A standard experimental test run produces test results where the main contributing factor of the resulting coating thickness is difficult to determine, partly due to some parameters that are unknown (local gas flow distribution etc.). Those parameters may be impossible to measure without affecting the CVD process. Thus, a high number of test runs would be needed in order to determine any main contributing factors. By using Comsol a commercial CVD system was modeled. The model was verified by in-situ temperature measurements in the CVD system at varied gas flows of different gas compositions with thermo couples. The in-situ measurements confirmed the Comsol model to predict the temperature and the CVD system. Two models of the system were used. First the whole CVD system was simulated in order to obtain the local conditions for gas flows and temperatures. Secondly, a smaller system was used that represented a ~1/30:th of the whole system, i.e. a single tray. The full system consists of about 30 trays stacked vertically. On the single tray the local gas flows and temperatures around each insert is simulated and ultimately the chemical reactions on the surface of the inserts can be simulated. The knowledge obtained from these simulations are used in changing hardware setup (heat exchanger etc.) and optimizing gas flows with regards of homogeneity of flows and temperature throughout the CVD system. Simulations of a CVD process with relatively good thickness distribution but weaker orientation of the crystals with a CVD process with poor thickness distribution and highly oriented crystals shows that low gas flows are beneficial for a homogenous temperature distribution inside the CVD reactor. The homogenous temperature distribution results in good thickness distribution. Since both good thickness distribution and highly oriented grains are desirable, alternative hardware setups are simulated with the aim to improve the temperature of the incoming gas for CVD processes with high gas flows. Three different hardware setups are presented of which two were interesting enough to proceed to real CVD experimental runs. The Comsol CFD simulations enabled rapid significant progress of the CVD hardware setup at a fraction of the time and cost traditional experimental test runs would have required.
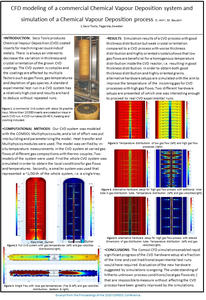