Multiphysics Simulation of Chaotic Mixing in Microfluidic Devices
Fast mixing of reagents in microfluidic devices is important for DNA sequencing, mRNA vaccine production in small-batch pharmaceutical processes, and point-of-care diagnostics. A key challenge in microfluidics is mixing reagents rapidly in a minimal amount of space. One way to do this is via chaotic mixing induced by geometrical features such as bends, turns, and grooves. In this study we use computational fluid dynamics (CFD) simulations to evaluate the mixing of ethanol and water over a range of flow rates for three common microfluidic chaotic mixer designs: serpentine, ring, and herringbone. All CFD simulations in this study were performed in COMSOL Multiphysics® with the Laminar Flow and Transport of Diluted Species interfaces.
The serpentine mixer (Figure 1) contains S-shaped channel segments that create a tortuous flow path. At low flow rates, the flow is purely viscous and mixing between the two fluids is dominated by molecular diffusion. Increasing the flow rate generates recirculation driven by inertial forces that enhance mixing. Figure 1 includes streamlines colored by relative concentration as well as concentration distributions at various channel cross-sections to visualize the degree of mixing, which increases progressively along the channel.
The ring mixer (Figure 2) operates by a similar principle as the serpentine mixer. The curvature of the rings exerts centrifugal forces on the fluid that, provided the flow is sufficiently strong, create counter-rotating vortices in the cross-sectional plane transverse to the main flow. This special type of inertial secondary flow is called "Dean flow."
Unlike the serpentine and ring mixers, the herringbone mixer (Figure 3) does not require fluid inertia. Herringbone mixers are designed with asymmetric, alternating grooves in the channel floor that induce counter-rotating fluid motions along the direction of flow. These secondary flows stretch and fold fluid elements periodically such that the distance between adjacent fluid layers halves with each cycle, a process known as the "baker's transformation." The thickness of the layers decreases exponentially after many cycles of stretching and folding, producing a homogeneous mixture.
The mixing efficiency of each device is quantified by the mixing time, defined here as the time required for the coefficient of variation of the ethanol mass fraction to be cut in half. The coefficient of variation is the ratio between the standard deviation and the mean of the ethanol mass fraction in the channel cross section. The mixing time is plotted in Figure 4 for each device as a function of the Reynolds number, which is proportional to the flow rate. The serpentine and ring mixers demonstrate efficient mixing at high flow rates (strong inertia), whereas the herringbone mixer exhibits short mixing times across a much broader range of flow regimes.
In conclusion, our simulations show that the herringbone mixer exhibits superior mixing performance over a larger operating window compared to the serpentine and ring mixers. Simulations such as these can be used to design the geometry and inlet flow rates of microfluidic mixers to optimize their performance, thereby reducing development time and cost.
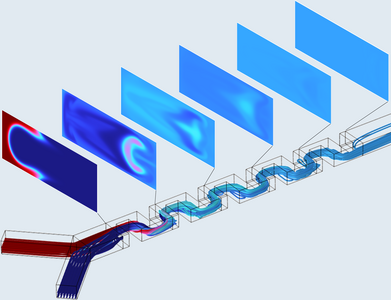