Numerical Simulation of Melt Hydrodynamics in Laser Micro Processing using COMSOL Multiphysics®
Laser material processing at micro-meter domain can be used for a plethora of applications such as micro drilling, micro welding, micro cutting, micro-texturing as well as micro polishing. These processes are governed by the time varying, complex melt hydrodynamics courtesy of melting and vaporization under high intensity laser irradiation. The melt pool convection results in geometrical defects such as recast layer, porosity, spatter formation, humping, protuberances and melt ripples. Thus industry utilization of such processes becomes difficult with mere experimental optimization. Therefore, a thorough understanding of physical phenomena associated with the melt pool is required. For that purpose, a numerical model has been developed as a predictive tool having adaptability in terms of various laser processing operation in commercial software COMSOL Multiphysics®. The salient points of the developed model are explained below
- The model takes into account all three phases: vapor, liquid (melt pool) and solid.
- The physical effects such as vaporized mass flow, recoil pressure, surfactant induced Marangoni convection, surface tension, and gravity have been incorporated.
- In terms of adaptability, the developed model can be applied to laser micro drilling (with pulse width of laser ranging from ns to CW), laser micro texturing, laser micro welding (conduction & keyhole mode, dissimilar materials), laser fusion cutting and laser polishing. At present, the choice of material is restricted to metals.
- The model uses fundamental physics module such as heat transfer, and laminar flow for setting up the basic model.
- The highly dynamic vapor-liquid melt surface is modelled using ALE (moving mesh), Phase field/ Level set interfaces. The choice of interface tracking module depends on the nature of the laser processing operation.
- The other facets of the Multiphysics problem such as calculation of surfactant concentration and different species of material are handled with the help of PDEs in mathematics module.
- The model tackles Laser absorption using Fresnel absorption (with temperature dependent optical properties) and the shadowing effect is incorporated using interface parameters.
- In line with the concept of digital twin in the laser manufacturing industry, a scaled-down 2D axis-symmetric universal model (preserving aforementioned factors) is presented, in which adaptive mesh refinement is employed to reduce the computational time (< 6 hours) for providing quick geometrical predictions.
In this paper, after a brief description of the developed model, simulation results on various laser processes such as laser micro drilling, laser micro welding, laser micro cutting, and laser polishing are presented along with a comparison with experimentally obtained data.
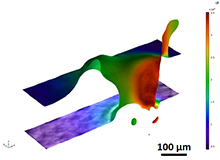
Download
- Shashank.pdf - 0.9MB