The SoftPad: a soft layer for adding compliance to the environment in robotic manipulation tasks
Soft robotics is an emerging research field that is rapidly expanding as soft robots are adaptable, reliable, and intrinsically safe. While the behavior of robots composed of rigid links, joints, and actuators can be easily described with classical mechanics modeling methods, modeling tools for soft robots are less exploited, and more complex to manage, as these devices are made of materials having highly non-linear behaviors. Having accurate models for soft robots, however, is very important to properly design them. In this abstract, we rely on accurate Finite Element Analysis (FEA) to study the behavior of a novel soft robotic component, called SoftPad. The SoftPad is a matrix of silicone pneumatic modules connected to pressure sensors that, when placed beneath an object, can be used to detect object pose, shape, and center of mass based on pressure variations [1]. Given the estimated center of mass, a planner computes the center and the direction of grasp that can be used by a robotic gripper to pick the object up. Thanks to the SoftPad, grasps can be performed without the need of a camera to locate the object and without prior knowledge of its mass distribution or its shape. Additionally, the gripper can safely interact with the soft surface, as its contact with it can be detected by reading pressure variations inside the SoftPad. Using the FE simulator provided within COMSOL Multiphysics®, in [2], we tested several material models available in the Nonlinear Structural Materials Module of COMSOL Multiphysics® to understand which one is most suitable for describing the functioning of a single module of the SoftPad. In particular, we compared the performance of hyperelastic material models including Neo-Hookean, Mooney-Rivlin, Ogden, Varga, and Yeoh and we found that Neo-Hookean and Yeoh are the ones that best predict the deformation of the SoftPad as a function of the inflating pressure. The SoftPad is made of Ecoflex 00-30 silicone rubber and its material properties were used to define the models coefficients. The FEM simulation conducted with COMSOL Multiphysics® also allowed us to study the variation of stiffness and sensitive area of the SoftPad modules. The SoftPad concept is a first step towards the instrumentation of the environment with soft inclusions for exploiting extrinsic, adaptable compliance during grasping and manipulation tasks performed by robotic grippers. The possibility of accurately modeling its behavior with COMSOL Multiphysics® will allow us to evaluate the interplay between different parameters (size, material, inflating pressure, etc.) in simulation before actually building the prototype, thus leading to an efficient process of interactive design.
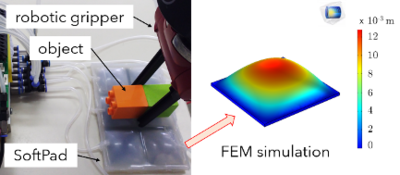
Download
- COMSOL_SOFTPAD_POSTER.pptx - 0.3MB