Ply Drop-off in a Composite Panel
Application ID: 90431
This example illustrates the modeling of ply drop-off in a composite panel. The panel considered for the analysis has three sections–thick, taper, and thin. The thick section plies are divided into the core, top-bottom belts, and dropped plies. The thick section of the panel has sixteen plies with symmetric angle-ply layup out of which eight plies are dropped gradually in the taper section with some specified stagger distance.
The carbon-epoxy material having transversely isotropic material properties is used as a ply material. The epoxy material having isotropic material properties is used in the pockets near dropped plies. The layerwise theory based approach together with the stack zone modeling is used for the detailed representation of the ply drop scenario. A stationary analysis is performed to compute stresses in different plies in various sections of the composite panel under the applied external load.
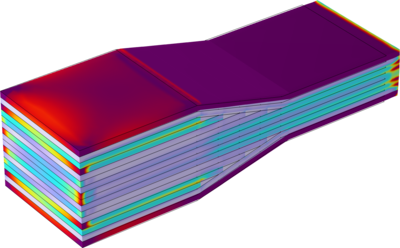
This model example illustrates applications of this type that would nominally be built using the following products:
however, additional products may be required to completely define and model it. Furthermore, this example may also be defined and modeled using components from the following product combinations:
- COMSOL Multiphysics® and
- Composite Materials Module and
- either the MEMS Module, or Structural Mechanics Module
The combination of COMSOL® products required to model your application depends on several factors and may include boundary conditions, material properties, physics interfaces, and part libraries. Particular functionality may be common to several products. To determine the right combination of products for your modeling needs, review the Tabella delle Funzionalità and make use of a free evaluation license. The COMSOL Sales and Support teams are available for answering any questions you may have regarding this.