A 3D Model of a Diesel Particulate Filter
Application ID: 1845
Several factors influence a diesel particulate filter’s (DPF) efficiency and durability. Important issues include the removal of soot particles from the filter membranes and the influence of thermal stress on the ceramic structure, stress that arises during repeated operating cycles. Mathematical modeling provides a powerful tool for investigating such critical parameters under a wide range of operating conditions.
This example studies the averaged flow field, concentration, and temperature distribution in a model of a DPF. The walls are porous, allowing gas to pass through them while at the same time separating particles from the flow.
The model sets up and solves the coupled flow plus mass and thermal balances describing the transport/reaction phenomena where the membrane is described using effective transport properties.
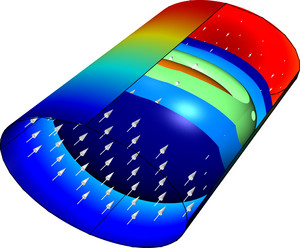
This model example illustrates applications of this type that would nominally be built using the following products:
however, additional products may be required to completely define and model it. Furthermore, this example may also be defined and modeled using components from the following product combinations:
The combination of COMSOL® products required to model your application depends on several factors and may include boundary conditions, material properties, physics interfaces, and part libraries. Particular functionality may be common to several products. To determine the right combination of products for your modeling needs, review the Tabella delle Funzionalità and make use of a free evaluation license. The COMSOL Sales and Support teams are available for answering any questions you may have regarding this.