Convective Evaporation of a Water–Acetone Droplet
Application ID: 125201
This model describes the evaporation of a droplet that consists of concentrated solution of acetone and water. It accounts for the coupled phenomena of chemical species transport and heat transfer over phase boundaries (liquid-gas boundary) as well as for multiphase flow.
The droplet is subjected to an impinging jet of a gas with a specified relative humidity. The vapor pressure of water and acetone at the droplet surface is higher than that of the impinging jet, thus causing evaporation. This evaporation is accelerated by the jet due to flow along the droplet surface. The heat of evaporation is also included in the model, and the droplet temperature subsequently decreases during evaporation. Acetone evaporates faster than water, due to its higher vapor pressure. This also implies that the composition inside the droplet changes over time. The droplet decreases significantly in size until most of the acetone is gone from the droplet. When only water remains, the droplet evaporates at a slower rate.
The model is defined by combining functionality for vapor–liquid equilibria, fluid flow, heat transfer, and moving mesh.
A Transport of Concentrated Species interface is used to solve for the mass transport in both the vapor and the droplet. The Vapor-Liquid Mixture Interface feature defines the vapor–liquid equilibrium at the droplet surface. The vapor pressure values are obtained using the Thermodynamic System feature. A Laminar Flow interface is used to solve for the fluid flow in the vapor and the droplet. A Fluid-Fluid Interface feature, together with a Moving Mesh interface, is used to track the droplet surface position, while also accounting for the evaporative mass transfer. Finally, a Heat Transfer in Fluids interface is used to solve for the temperature in the vapor, liquid, and in the marble on which the droplet is placed. Composition-dependent properties defined are used both in the vapor and in the liquid.
The model includes two studies. The first study is used to initialize the droplet shape. Here, only the fluid flow and moving mesh are solved for. In the second step, evaporation is modeled by solving for all coupled physics interfaces as well as tracking the interface.
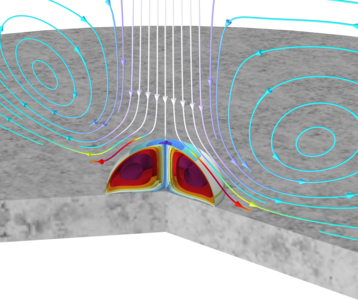
This model example illustrates applications of this type that would nominally be built using the following products:
however, additional products may be required to completely define and model it. Furthermore, this example may also be defined and modeled using components from the following product combinations:
The combination of COMSOL® products required to model your application depends on several factors and may include boundary conditions, material properties, physics interfaces, and part libraries. Particular functionality may be common to several products. To determine the right combination of products for your modeling needs, review the Tabella delle Funzionalità and make use of a free evaluation license. The COMSOL Sales and Support teams are available for answering any questions you may have regarding this.