2-D Modeling of CO2 Electrolysis Using Gas Diffusion Electrode Operate at Neutral pH and Mild Conditions
CO2 capture and further conversion into valuable products can be a promising solution against global warming. Normally, CO2 conversion can be achieved by chemical methods, by photocatalytic and electrocatalytic reduction [1]. Specifically for electrocatalytic reduction of CO2, challenges remain, such as the slow kinetics of CO2 electro-reduction, even when high electrode reduction potential are applied. It has been recognized that the biggest challenge in CO2 electron reduction is low performance of the electrocatalysts (i.e., low catalytic activity and insufficient stability) [2]. Several metal catalysts have been used, ranging from their selectivity and product desire (Pt, Pd, Cu, Sn, Ag, etc) . Interestingly, non-noble catalyst, specifically (M-N-C) groups show prominent stability and activity towards CO2 reduction reaction [3,4]. Enhanced performance in electrochemical cells can also be realized by modifying conditions of operation, e.g. temperature and pressure, and by exploring alternative cell designs. For example, if we consider a CO2 reduction using saturated electrolyte. The low solubility of CO2 in water (e.g 3 mM at 25 C at 1 bar pressure of CO2) means the current density is typically limited by diffusion of CO2 to the electrode surface. To try to reduce this mass transport limitation, operation at high pressure, increase CO2 solubility by adding chemical compounds or the use of gas diffusion electrodes [5]. For Ag, Au, Zn, In, Pb, Sn and Bi, high pressure improves the Faradaic efficiency for CO and/or HCOOH, but product selectivity is unchanged. In order to gain industrial interest reduction current should be higher than 100 mA cm-2.[6]
The Co-electrolysis single cell consists of seven sequentially connected domains: anode/cathode inlet/outlet channels (AC/CC), anode/cathode Gas Diffusion Electrode (GDL), anode/cathode catalyst layer (CL), and the electrolyte. For all of these domains, we accounted for various phenomena affecting the behaviour of the cell and we incorporated in the model interlinked main sub-models: the mass transfer sub-model (MT: Maxwell-Stefan equation) for dynamic mass transport, the fluid-dynamics sub-model (FD: Navier-Stokes Brinkman), the heat transfer sub-model (HT: Maxwell-Stefan equation) for energy balances, and the electrochemical sub-model (EC: Butler-Volmer with concentration depended) for charge balances in anode and cathode CL. All implemented equations are solved within the various domains, and connected by sources terms. We realized a 2D geometry of the entire single cell by using the CAD kernel in COMSOL Multiphysics® with parametric values (lengths, depths, heights, etc.). We implemented different meshes with increasing number of tetrahedral elements for the various domains to better represent the structural interactions between adjacent domains. [7]
In this work, the production of syngas was selected as our target desired product. A sensitive analysis of the Co-electrolysis process using several electrolytes, temperature and pressures have studied. The thickness of the electrolyte and electrodes domains were varied and evaluated their effect on the cell performances. The final propose is to compare experimental data (work in process) with our model and optimizing the CO2 co-electrolysis process.
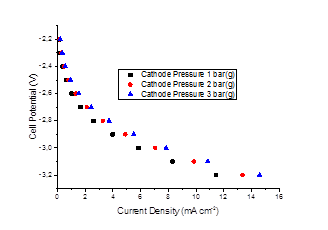
Download
- videla_abstract.pdf - 0.03MB