A Heat Transfer Simulation for Heat Management in the Design of a New ReactorSTM
With the ReactorSTM the relationship between surface structure and catalyst activity under industrially relevant conditions can be investigated. It enables atomic-scale observations of model catalysts under conditions approaching those used by the chemical industry. It consists of a compact STM scanner, of which the tip extends into a 0.5 ml reactor flow cell, that is housed in an ultra-high vacuum (UHV) system. The setup combines a scanning tunneling microscope (STM), partly integrated into a small flow cell, with a UHV system that is equipped with standard surface preparation techniques, such as ion bombardment and metal deposition. The ReactorSTM enables us to study the surface structure of a catalyst in combination with simultaneous mass spectrometry and thereby to directly correlate structural changes with chemical activity [1]. The current design withstands 600 K and 6 bar. By developing a new version of the microscope operating at higher temperature and pressure, we will be able to investigate more catalytic reactions. To reach this goal, understanding of heat transfer inside the ReactorSTM is the first step.
Heat transfer simulations and temperature profiles in our ReactorSTM are achieved by performing finite element analysis (FEA) calculations with COMSOL Multiphysics®. In practice, it is not easy to measure the exact temperature of the scanner and piezo part of the microscope in our reactor, since all the equipment is located in the ultra-high vacuum chamber. COMSOL Multiphysics®, with a dedicated module and ability to set boundary conditions, can predict the maximum temperature of the piezo scanner while the catalyst is at high temperature. For the simulation, heat transfer in solid and fluid coupled with the surface-to-surface radiation interface in a 2D axisymmetric dimension and under stationary conditions has been used.
The simulation results using COMSOL Multiphysics® illustrated that changing catalyst materials contributing to conductive heat transfer had no effect on the temperature profiles inside the reactor. However, pressure, velocity, and composition of gases affecting convective heat transfer play a major role in the heat distribution inside the reactor. Among different parts of the ReactorSTM, the current seal and piezo tube will not be able to resist the high temperature of the catalyst surface (1200 K) in high pressure (12 bar) and high velocity (0.1 m s-1) of gas. Also, increasing gas velocity and pressure show a dominant contribution to the convective heat transfer.
1. C.T. Herbschleb et al., Rev. Sci. Istrum. 85, 083703 (2014)
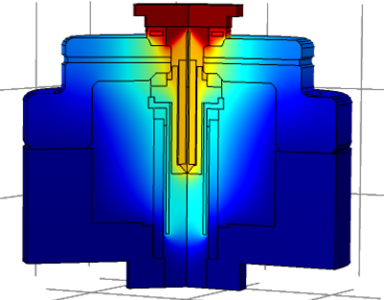