Analysis of Mechanical Sensitivity of MEMS Pressure Diaphragm for Contact Formation
MEMS Pressure sensors work on the principle of mechanical bending of thin diaphragm under applied load over diaphragm area. The sensitivity of diaphragm is crucial to efficiency of the sensor. It is defined as the increase in deflection of diaphragm as a result of increase in pressure acting on diaphragm. Single diaphragm under atmospheric pressure becomes stiff upon deflection. To avoid stiffening, this unique design provides a diaphragm and a rigid structure for use with a MEMS transducer, Figure 1. To improve mechanical sensitivity different corrugation techniques were also used using Polycrystalline Silicon and Silicon Nitride as diaphragm materials. But only Polyimide has advantage of very low Young`s modulus (2.5-3.1GPa) compared to Polycrystalline Silicon (160GPa) and Silicon Nitride (250GPa). The diaphragm consists of a thin first layer formed of metal designed to hold encapsulated pressure and has thickness of few hundred nanometers. The second layer is polyimide and is thicker (2um) than first layer. The rigid structure is of Polycrystalline silicon material with thick boss (10um) suspended using very low stiff spring structure for high mechanical sensitivity. The diaphragm lies below the rigid structure with a gap (5um) and extends and retracts in response to changes in atmospheric pressure. The rigid structure and diaphragm is encapsulated under 1 atmospheric pressure. First part of our analysis is based on assumption, which one can think of in simplest cases, to calculate mechanical sensitivity when atmospheric pressure (Patm, over 100% radius) and encapsulated pressure acting over rigid structure (Pext, over 90% radius) act simultaneously on diaphragm opposite boundaries. Contact simulation is not involved here. The second part is done with realistic non-linear contact simulations where diaphragm and rigid structure boundaries form contacts under applied loads. The contact area also plays an important role in determining sensitivity. A 2D axisymmetric model is implemented in the Structural Mechanics Module in the COMSOL Multiphysics® software. The COMSOL Multiphysics® simulation software helped solving the non-linear problem using Newton Raphson iterative technique and utilizing load ramping concept with computationally robust Augmented Lagrangian contact solver. Mesh refinement is done for source and destination boundaries. The stress stiffening effect has been taken care of by removing geometric non-linearity from everything except contacts. The dimensions, material properties and intrinsic stresses (100MPa & 1MPa) are set for the two cases. The mechanical sensitivity for the first case is analyzed using different materials and choosing different intrinsic stress values. To reduce the stiffness of diaphragm, atmospheric pressure exerted on the second layer generates concentrated stresses while exposing rigid first layer to distributed stresses. It gives six times higher mechanical sensitivity than Polycrystalline Silicon diaphragm of same specification. The rigid structure is designed to be highly sensitive than the diaphragm. But how the sensitivity will turn out after contact formation is determined using simulation. The second results show the contact analysis gives much lesser sensitivity. The reason for significant difference can be pointed to behavior of contact parts moving as a thick structure unit after contact establishment and hence drop in sensitivity.
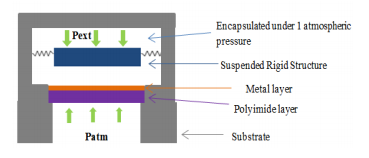
Download
- shubham_presentation.pdf - 0.91MB
- shubham_poster.pdf - 0.39MB
- shubham_paper.pdf - 0.31MB
- shubham_abstract.pdf - 0.03MB