Comparison of Diffusion Flux Models for Fischer-Tropsch Synthesis
The Fischer-Tropsch Synthesis (FTS) is a highly exothermic condensation polymerization reaction of syngas (CO+H2) in the presence of Fe/Co/Ru-based catalysts to produce a wide range of paraffins, olefins and oxygenates, the latter of which is often called syncrude. Multi-Tubular Fixed Bed Reactors (MTFBR) and Slurry Bubble Column reactors (SBCR) are widely employed for FTS processes [1]. To understand the reactor-scale catalyst performance, it is important to first analyze particle-scale transport-kinetic interactions. The FTS reaction network produces hydrocarbons with carbon numbers typically ranging from 1 to 100 so the catalyst pores in this process can be potentially filled with liquid wax (C20+) leading to high diffusional limitations. To model such a reaction network and account for all species, micro-kinetic rate expressions for each individual species must be coupled with the intraparticle solubility of gases in liquid wax and transport equations for the various reaction species in the porous catalyst. Temperature based correlations for diffusivities of FT products in wax are widely used and a comparison of diffusion flux models (Wilke, Wilke-Bosanquet, Maxwell-Stefan, and Dusty Gas) to describe species transport-kinetic interactions for FTS has not been reported in literature. A 2-D particle model for different catalyst shapes (solid cylinder, hollow cylinder, 4-hole cylinder, modified 4-hole cylinder and 7-hole cylinder) was simulated to compare the particle-level performance for the gas-phase FTS. A Fe-based micro-kinetic olefin re-adsorption model developed by Wang et al. (2008) was coupled with the Soave-Redlich-Kwong (SRK) equation of state to describe the particle-scale transport-kinetic interactions and phase behavior for the gas-phase FTS [2]. The diffusion flux models, intra-particle effectiveness factor, liquid-to-vapor ratio, CO conversion and intra-particle volume-averaged concentration of diesel were analyzed at different process conditions to compare the performance of different catalyst particle shapes. This work describes the initial results obtained from such an effort using COMSOL Multiphysics® software as the numerical engine for solving the model equations.The 2-D isothermal intra-particle concentration profiles of diesel (C13-C17) for different catalyst particle shapes are shown in Figure-1.
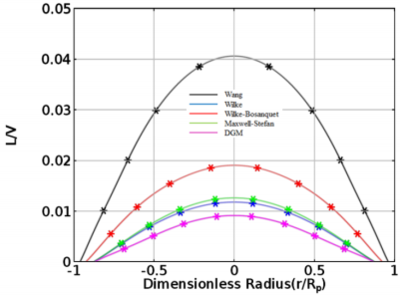
Download
- nanduri_presentation.pdf - 2.12MB
- nanduri_poster.pdf - 1.66MB
- nanduri_paper.pdf - 0.64MB
- nanduri_abstract.pdf - 0.1MB