Design and Optimization of Power Cable Accessories Using COMSOL Multiphysics®
Power cable manufacturing is limited by the maximum length of cable that can be produced and stored on cable drums. This creates a need or rather an opportunity for a cable accessory, namely 'Cable Joints'. Joints are an impeccable component in the power cable network that necessitate extreme care in their design and installation in order to facilitate a smooth connection between two cable ends and to reduce the chances of failure. However, design and optimization implies repetitive testing through trial and error which proves to be an expensive process as we move to higher voltage levels. There are several standards such as the IEC 60287/HD 629.1/IEEE 404 that govern the testing and validation of such cable joints. However, software packages such as COMSOL Multiphysics® help simulate the problem domain as close to the real world problem by enabling the coupling between different physical phenomena. The very fact that electric and magnetic fields are never ideal calls for the need to visualize the actual potential and field distributions over the problem space. Further, the design is easily optimized by changing the CAD geometry using a LiveLink™ interface.
This paper demonstrates the overall process of modeling and optimization involved in the design of a power cable joint by Lovink Enertech B.V. with the aid of the COMSOL Multiphysics® software and its relevant modules. It involves the extensive use of the AC/DC Module and Structural Mechanics Module. Using these two modules and the multiphysics couplings available in COMSOL it is possible to make electrostatic, thermal and thermal expansion calculations at steady state and magnetic and mechanical estimations in transient cases.
Through the electrostatic calculations, the electric field control part of the joint is validated and the design is checked for any undesired electric field enhancement. Electrostatic simulations are the most important among all, as they help to verify the electrical robustness of the design. Together with magnetic field simulations it is possible to check the regions where energy transfer takes place and in turn simulate the thermal behavior of the component under test. The thermal behavior of the joint is very important part of the design process and the simulations follow the standards defined by the IEC. On the contrary, magnetostatic simulations are slightly tricky in this case and require the use of an in-plane vector solution together with a scalar for gauge fixing in order to obtain the right results. The detailed process is described in the complete paper.
As an additional step, simulations were performed for mechanical expansion and pressure build-up within the joint due to Joule heating, and short circuit tests were simulated to obtain the maximum forces experienced by the joint. The complete paper describes them all in detail.
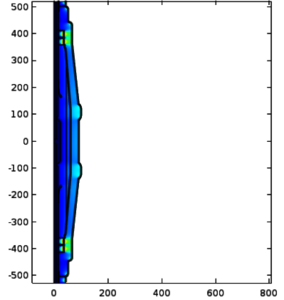
Download
- lewarkar_poster.pdf - 0.84MB
- lewarkar_paper.pdf - 0.62MB
- lewarkar_abstract.pdf - 0.05MB