Extended Physics Modeling of the Resin Flow During Vacuum Infusion Processes
Vacuum infusion processes are well adapted for large composites parts and, therefore, widely used for the manufacturing purposes in several applications fields such as aviation or naval industry. Simply speaking single plies or a given fibrous reinforcement is pre-shaped and positioned into a mold and tightly separated from the environment by a vacuum bag. The resin flow during the infusion process is driven by the applied pressure gradient between inlet and outlet. Common simulation packages for industrial application are using a single phase flow formulation of the Darcy law, from which the proper representation of critical physical properties enabling a realistic prediction of the impregnation is not achieved. In many cases the accuracy of results obtained with this basic calculation method is not acceptable. For better understanding of the process and more precise prediction of resin flow, the influences of other physical parameters have to be included. This is an enabler for improving processes and for faster, more efficient and more reliable production of large scaled CFRP parts in vacuum infusion technology.
In this study the classical approach formulation of Darcy’s equation for flow in porous media is coupled with the influence of capillary forces at the flow front: According to Darcy equation at a constant pressure gradient, calculation shows a continuing resin flow until the outlet is reached. Here the pressure is generally set to zero. As the pressure gradient is only driven by the distance between inlet and outlet, it remains constant and the resin flow front will never stop before passing the outlet. In opposite it can be observed from experiment, that flow front stops moving at a critical distance. It is assumed that capillary forces contrary to pressure gradient slow down the resin flow and describe in that way an additional dissipation mechanism for the total flow energy (momentum). Dedicated experiments are designed and performed for quantifying the critical flow distance under real process conditions. Based on the recorded transient evolution of the flow front position, the velocity of resin during the process is determined. Afterwards Jurin’s law for capillary forces is used for calculating the decrease of velocity. Darcy’s law and Jurins’s law are coupled for calculation of simulation of the flow. The objective is to get a flow simulation with a stopping flow front according to the experimental data.
Using COMSOL Multiphysics®, resin flow in porous media is calculated with the Darcy's Law physics interface of the Subsurface Flow module. The weak form of partial differential equation is used for implementing the capillary force. By coupling of both nodes, the resulting flow front velocity is determined. The flow front tracking was implemented using the Level Set approach from the mathematics interface. So the motion of resin can be visualized. Corresponding to the experimental setup a 3D model is used.
The study shows the implementation of additional influences on the classical flow in porous media. Based on that, other physical impacts will be considered to provide a more precise simulation environment for the industrial process.
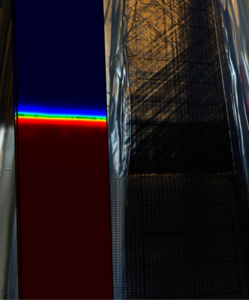
Download
- stolz_presentation.pdf - 0.5MB
- stolz_poster.pdf - 0.45MB
- stolz_abstract.pdf - 0.32MB