Framework for in-process thermal analysis in COMSOL for free-form FFF printing.
Hot material extrusion (MEX) additive manufacturing with filament feedstock (also known as fused filament fabrication (FFF) or fused deposition modeling (FDM™)) is one of the most popular and fast-growing 3D-printing techniques for consumer and educational purposes. A continuous thermoplastic filament is extruded through a hot nozzle and selectively deposited onto an existing anchor (build plate or previously deposited part) to construct 3D printed parts typically in a layer-by-layer manner. The simple handling and limited required technological and financial investment make this technology attractive for a wide range of end-users, from non-professional to industrial-level stakeholders. As a thermally driven process, a deep understanding and prediction of the in-process temperature of the deposited strands (build temperature) is critical in FFF to ensure reliable and quality results. Simulating thermal information can then help predicting and implementing suitable printing strategies to ensure part performance and production efficiency. In-process temperature simulations and numerical models have already been developed and verified for FFF-printing. Zhang et al. and Ferraris et al. developed a tool called T4F3 to calculate the in-process filament temperature during printing for square shaped parts [1], [2], [3] by solving an initial and boundary value heat transfer problem in a changing domain with the finite difference method. D’Amico and Peterson used the COMSOL’s software to simulate material addition with the “Deformed Geometry” node [4]. Nain et al. [5] used the material activation method, available in the Structural Mechanics Module of COMSOL, to model the material addition of the process. All these investigations focussed on simple shapes or only one type of material.
In this research, an investigation is made to assess the use of COMSOL Multiphysics in developing thermal simulation of the FFF-printing process. After this a framework is set up for the modelling of free-form prints. A CAD-model of varying shape, from a simple figure to a complex profile, is imported into COMSOL. The corresponding G-code is converted with Matlab and imported to activate material at given printing temperatures, depending on the used materials (PLA and PETG). Conduction with neighboring strands and convection/radiation with the environment are modelled to investigate the temperature of each segment of filament deposited. These results are validated with the numerical model T4F3 and compared to experimental monitoring with an infrared camera.
COMSOL Multiphysics helps investigate the thermal characteristics of free-form parts printed with FFF printers. This is the next step towards physics-informed adaptive printing strategies, improving quality and printing time. The identified simulation strategy can then be applied to more complex profiles and bulk geometries for free-form investigations.
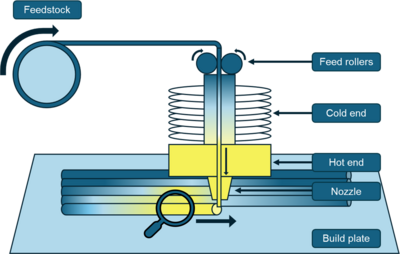
Download
- abts_11181_poster.pdf - 2.24MB
- 3_robrecht-abts.pdf - 1.1MB