Friction Factor for Perforated Pipes
Perforated pipes are extensively used to control exhaust noise in automobiles [1-4]. The energy loss associated with the perforations leads to back pressure which needs to be quantified and minimized [5]. An objective approach presented in [6] is the introduction of friction factor for perforated ducts as a function of the porosity. In this article, the utilization of the CFD Module of COMSOL Multiphysics software to conduct numerical experiments is elaborated in detail.
The study is carried out by using the normalized pressure drop (Pressure drop divided by dynamic head) as the performance parameter. The effect of various parameters like the porosity, pipe thickness, hole diameter, pipe diameter and pipe length are studied through parametric studies. It is observed that the effect of pipe thickness, hole diameter, pipe diameter and pipe length is practically negligible. Consequently, a relationship is sought between the normalized pressure drop and the porosity. Finally, the friction factor for perforated pipe is deduced. The result so obtained is validated by comparing the pressure drop of the concentric tube resonator with previously published literature.
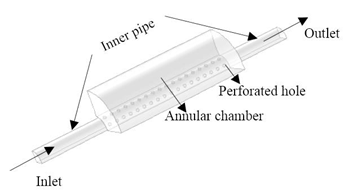
Download
- neihguk_poster.pdf - 0.46MB
- neihguk_abstract.pdf - 0.07MB