Impact of the Forces due to CLIQ Discharges on the New HL-LHC Beam Screen
In the framework of the high luminosity large hadron collider (HL-LHC) project, important upgrades will take place by 2024 including the installation of new superconducting magnets in which new beam screens will be placed. The beam screen is an octagonally shaped pipe inserted into the cold bore of superconducting quadrupoles a few tens of meters from the proton beam interaction points (ATLAS and CMS). It ensures vacuum stability by means of small holes along its uncovered surfaces, and shields the 1.9 K magnet cryogenic system from the heat loads and damage to the coils that would be otherwise induced by the highly penetrating collision debris. This is obtained by dense tungsten blocks placed on four of the flat surfaces of the screen. The remaining surfaces accommodate four cooling capillaries whose purpose is to transfer the heat absorbed by the tungsten to the capillaries through highly conductive thermal links.
The main subject of this study concerns the investigation of the magnetic, thermal, and mechanical behaviours of the beam screen during a potential failure of LHC, namely, a magnet quench. This phenomenon results in a resistive transition of the superconducting magnets, which calls for a protection system whose reliability is particularly challenging due to the high stored energy per unit volume of coil. In this case, the beam screen has to guarantee its mechanical integrity to ensure the operation of the accelerator.
A numerical FEM (Finite Element Method) model has been developed using COMSOL Multiphysics® to quantify the eddy currents and the resulting Lorentz forces induced by the rapid magnetic field decay of the new quadrupole magnets. The model takes into account a new quench protection system known as CLIQ (Coupling-Loss Induced Quench) under development at CERN. This system relies on a capacitive discharge, which causes inter-filament coupling losses that result in a reliable heating system. Such system is connected to the magnet circuits in a way that the current discharge of the magnet poles is not uniform. Therefore, the model has been developed by considering the poles as individual magnets whose magnetic field variation can be assigned arbitrarily. Moreover, as the induced forces depend on the electrical conductivity of the material which in turn depends on temperature, thermal analyses have taken into account the change of material conductivities as well as the temperature increase due to resistive losses. The most important outcome of the model is the evaluation of the induced forces, which are then deployed to assess the equivalent stress and displacement of all the assembly components. They, in fact, have to stay within certain safety values to protect the magnet coils in the vicinity of the cold bore, and the assembly itself. It has been shown that the CLIQ discharge leads to a torque load in the beam screen components hitting the cold bore not in a conventional way.
A beam screen prototype has already been manufactured according to the main results of the simulations and it will be tested by the end of 2017.
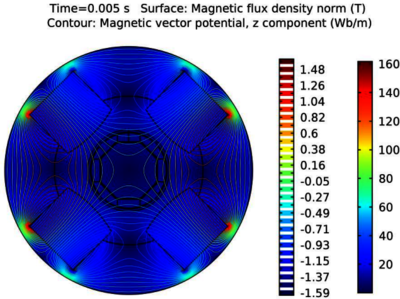
Download
- morrone_presentation.pdf - 2.67MB
- morrone_abstract.pdf - 0.02MB