Laser Assisted Bonding (LADB) Thermal Modeling with COMSOL Multiphysics®
New emerging trends in the MEMS market are linked to the availability of small, reliable and miniature sensors for harsh environment applications to increase penetration in all application fields, considering very wide operating condition ranges. These trends are pushed forward by the strong digitalization process of our societies (IOT and Industry 4.0 trends).
The key aspect in the MEMS packaging reliability is to reduce thermal mismatch of materials, mechanical stress and, in general, to ensure a robust solution and protect the sensor when operating in a defined environment condition. For example the operating temperature for a silicon carbide MEMS pressure sensor could be as high as 650 °C in air, for applications in the field of real-time engine pressure monitoring.
Material choice and micro-metallurgy are therefore also critical to achieve a robust MEMS technology and to find optimal packaging solutions. Protection of the MEMS transducer with a hermetic seal is crucial and must not generate reliability issues by itself. In CSEM a large effort has therefore been put to ensure laser bonding is performed with very localized heat and minimal damage to the sample, achieving low-stress and low-temperature hermetic sealing of any MEMS or MOEMS component.
COMSOL Multiphysics® simulations are presented here with the goal to optimize the hermetic sealing process and to avoid, for example, the overheating of the samples due to different package size and different material thermal behavior.
At last results have been compared to experiments, showing the progress in
understanding the physics behind the laser-based hermetic bonding and the
impact is to have a quantitative estimation on laser bonding (LADB) process parameter impact for different package design specifications and for different thermal scenarios.
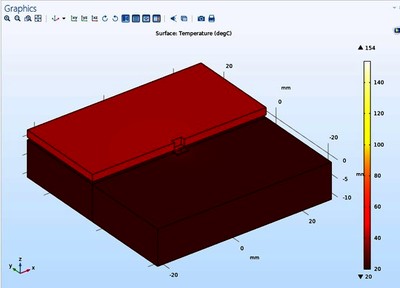