Micro cooling channel heat sinks designed by topology optimization
As a key component of MEMS, microprocessor with high computing performances is facing with severe thermal challenge due to the increasing power density, miniaturization as well as higher operating temperature requirements, and thermal management in corresponding fields has become one of the crucial issues. Micro channel heat sink integrated single-phase liquid cooling shows great potential regarding to the excellent heat dissipation capacity and low cost. However, the conventional micro cooling channel layout like parallel or serpentine (S-shaped) pattern has several significant drawbacks such as higher hydraulic resistance and higher temperature gradient, which means higher pumping power is required to remove high heat flux. In order to overcome these disadvantages of the conventional heat sink, the channel layout should be optimally designed to achieve better flow and thermal performances. In order to study the relationship between the flow and thermal performances and the layout of cooling channels designed by topology optimization from the engineering point of view, two types of channel layouts with different channel volume fractions are studied. The first is to achieve the minimization of power dissipation under the flow rate quality constraints, and the second is to achieve the maximization of heat exchange under the constant input power constraint. Then the optimized heat sinks together with the conventional S-shaped channel heat sinks are manufactured and their flow and thermal performances are investigated both numerically and experimentally. COMSOL Optimization module is used to solve the optimization problems, and CFD and Heat Transfer Modules are used to implement the finite element analysis of the fluid-thermal coupled system. The results reveal that the optimized channel design can enhance the flow and thermal performances of the heat sinks. The power dissipation minimization design provides the best temperature uniformity, while the heat exchange maximization design keeps the peak temperature to a minimum. Additionally, the coefficient of performance of the heat exchange maximization design is the highest among three types of layouts, which means it can remove more heat energy at the same pumping power.
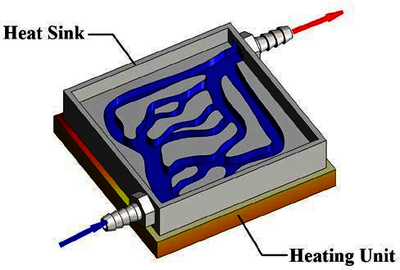
Download
- 李_presentation.pdf - 2.62MB
- 李_paper.pdf - 0.74MB
- 李_abstract.pdf - 0.16MB