Modeling the induction error in measuring furnace core voltages in metallurgical processes.
Accurate measurement of electrode loads is crucial for the optimal operation of a large 3-phase electric melting furnace. Generally, measurements are made by combining electrode current and voltage drop between the top of the electrodes and the core of the furnace. For this purpose, the core of the furnace has to be electrically connected to transfer its potential to a measurement device in the control room. However, this method raises problems due to induced voltages in the measurement apparatus caused by the strong magnetic field around the furnace which leads to erroneous readings.[1] To tackle this problem, a system consisting of three measuring leads is placed symmetrically around the furnace. The signal from these three leads is believed to provide destructive interference of induced voltage and a practical means of transferring the voltage of the initial point without inductive error. Although this method of measuring direct voltage is widely believed to be accurate in principle, it can be challenging to apply in actual industrial environments due to various hurdles and equipment issues. Moreover, it is unclear how this approach performs on furnaces with asymmetrical electrical conditions.
To address this gap in knowledge, our study aims to shed light on the reliability and limitations of this approach using a full 3D Finite Element Method model of an industrial-size furnace for primary metal production[2] implemented in COMSOL. Our model uses an idealized yet realistic distribution of the material and structural elements of the furnace. Electrical conditions are investigated exploiting the capability of the ACDC module (magnetic and electric field - mef) and an electrical circuit (cir) model tracks the true power for each phase. The model implements 36 unique leads as open curve polygons. For each lead path, integration along the defining edges of the tangential component of the electric filed give the induced voltage.
By examining the residual inductive errors of different lead arrangements under different conditions and investigating the impact of the electrical status of the furnace on measurement accuracy [3] we show that: a) symmetrical lead placement causes complete destructive interference of induced voltage when the electrical state of the furnace is balanced; b) material imbalances lead to only partial signal cancellation, resulting in a induction error that is in phase with the voltage at the core; c) adjustments to electrode positions to restore the balance of the electrical conditions also reduces the residual induction error.
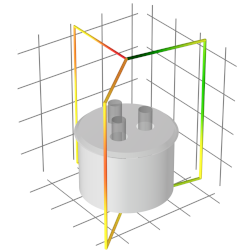
Download
- sparta_11001_poster.pdf - 1.54MB