Multi-Beam Mask Writer Magnetic Lens Optimization with Comsol Multiphysics
In order to facilitate semiconductor production in the upcoming technology nodes (3nm, 2nm, 14A) our state-of-the-art multi beam mask writer (MBMW) needs constant improvement in throughput and writing precision. As these two goals contradict each other, adaption of the electron optical system is required for each future tool generation. The aim of this work is to minimize lens aberrations that are unavoidable in rotational symmetric electron lenses while maintaining their imaging properties such as principal plane location and focal length. Lens aberrations in the projection system result in an increased electron beam blur that again limits pattern fidelity. We utilize Comsol Multiphysics in the Java programming mode, allowing the integration with existing software and analysis tools in our company. In this way, model input parameters, such as pole piece geometries and the input coil current of a lens system can be accessed and controlled by the automation software (Fig. 1a). On the other hand, the field export capabilities enable analysis in the aberration analysis environment. Fast FEM calculation with high accuracy is a key factor in the optimization procedure as the number of input parameters can be up to 20. In addition, the extremely high ratio between the model dimensions (m) to the desired beam precision (<nm) introduces a signifcant challenge in the modelling process. A combination of magnetic field (mf) and magnetic fields, no currents (mfnc) physics nodes is used (Fig. 1b) in order to utilize the quintic discretization of the latter, resulting in the required accuracy. Especially at the pole piece vertices and the region of the e-beam path the mesh needs refinement for best results (Fig. 1c). A single iteration of the lens optimization procedure is illustrated in Fig. 2. By following this approach with Comsol Multiphysics, we have successfully designed next-generation MBMW systems with excellent accuracy, as confirmed by tool experiments. The reduction in image field blur for the next generation of the MBMW by 30% is shown in Fig. 3.
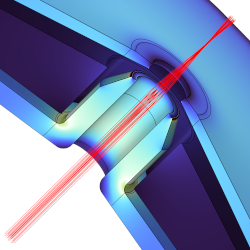
Download
- puchberger_10862_poster.pdf - 1.25MB