Multi-physical simulation of cryogenically cooled axial-flux electric motor
Axial-flux permanent-magnet motors are an important technology in many technical applications, being an alternative to radial-flux motors. Axial-flux motors come up with many advantages in comparison to radial-flux motors such as high-power density, higher torque to weight ratio etc. Although high efficiencies are achieved, energy losses lead to high temperatures in the motor assembly. Heat losses in an electric motor are mainly generated due to AC/DC losses and this in turn reduces the efficiency of the drive system. In the scope of the project K-AXFLUX, an attempt is made to develop an axial-flux motor (Fig. 1) which is cooled with hydrogen gas passing through the hollow conducting copper coils of the stator. Liquid hydrogen from a storage tank is pumped into the inlet of the conducting copper coil and is in gaseous state at the inlet of the copper coil. The hydrogen gas from the outlet of the coil is then further sent to the fuel cell, forming a continuous circulation loop. In the scope of this paper, a multi-physical simulation model of the stator geometry is developed to evaluate the cooling effect from liquid hydrogen flow and evaporation and the resulting temperature distribution within the stator geometry of the axial-flux motor.
In the simulation setup of COMSOL, the sectoral symmetry of the geometry is exploited to reduce the computational time and effort. Hence, a sectoral model (Fig. 2) is used for the multi-physical simulation and periodic boundary conditions are applied on either side of the sectoral model. The simulation model involves usage of the following COMSOL modules: turbulent flow of hydrogen in the hollow coil, heat transfer in solids in copper and heat transfer in fluids in air around coil. Further, non-isothermal multi-physical coupling is used to evaluate the temperature distribution of the stator geometry. The model is highly non-linear due to the material non-linearity and turbulent flow study. Therefore, the study is divided into multiple steps starting with fluid flow combined with auxiliary sweep and then solving heat transfer and fluid flow with the use of non-isothermal coupling.
The simulation provides detailed insights into the temperature profile, pressure losses and fluid flow velocity along the length of the copper coil. Through conduction and convection, heat is exchanged between the copper coil and the hydrogen gas, causing the fluid to heat up as it traverses the coil. This in turn leads to pressure drop across the length of the coil (Fig. 3). Importantly, the simulation results indicate that the copper coil maintains a temperature below 293 K throughout its length of the coil demonstrating the effectiveness of hydrogen as a fluid in internally cooling the coils. A lower temperature of the copper coil enhances electrical conductivity and reduces heat generated by resistive heating, thereby improving the motor's efficiency. Further, the temperature attained by the stator geometry and its surroundings is crucial for the motor design (Fig. 4).
The current simulation model serves as a foundation for further multi-parameter optimization using surrogate modelling and Bayesian optimization techniques, aimed at enhancing the thermal efficiency of the axial-flux electric motor.
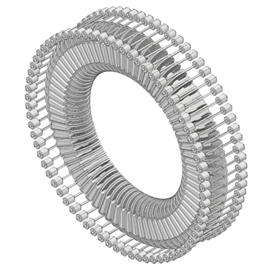
Download
- kamath_10771_poster.pdf - 0.55MB
- comsol_conference_paper_kamath.pdf - 0.54MB