Numerical Characterizations of Visco-Plastic Behaviour of the TA6V with Metallurgic Phase Change
In order to predict the residual mechanical state of assemblies during pulsed laser welding, mechanical and metallurgical behaviors of materials need to be precisely characterized. Based on experimental data and analyses [1], a numerical model is developed in COMSOL Multiphysics® software to take into account the predominant effects identified for TA6V.
First of all, the metallurgic behavior is modeled with two differential equations (“Domain ODEs”) by describing the kinetics evolutions of the metallurgic phase transformations. Two kinetics of heating and cooling are studied exhibiting the influence of this parameter.
Secondly, cycling tensile tests are numerically performed at different temperatures. A visco-plastic model with non-linear kinematic hardening is implemented in COMSOL to describe the thermo-mechanical behavior of the material. The visco-plastic strain as well as the “shift-stress” tensors are rewritten with differential equations (Domain ODEs) and the classical Solid Mechanics physics interface is used, as proposed in [2].
The full system is then solved with a segregated solver for a study case of tensile/compression. Different temperature levels are studied to characterize the material behavior on a representative range and to validate the numerical implementation. Based on the analyses described in [1] and on several simulations, all the constitutive parameters are expressed as a function of temperature. Experimental and numerical results are compared in Figure 1, in terms of strain/stress states, for 8 temperatures at a fixed strain rate (10^-3 s^-1).
Satisfying agreements are obtained in each case, validating this visco-plastic approach. This model can now be used to describe the thermal-metallo-mechanical behavior of the TA6V under industrial welding stresses.
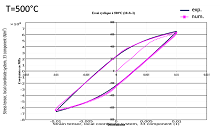
Download
- bruyère_presentation.pdf - 2.05MB
- bruyère_paper.pdf - 0.95MB
- bruyère_abstract.pdf - 0.61MB