Power tool battery packs: shortening intervals of operation & charging by improved cooling strategy
In the fast growing but also highly competitive market of battery-powered power tools short charging times are essential to achieve customer acceptance and to create unique selling propositions. To prevent loss of performance and fast charging capability due to cell aging, the knowledge of proper use conditions in everyday practice is important. At Aalen University, a COMSOL Multiphysics® model of an 18V power tool battery pack was developed to be able to evaluate different application scenarios of practical relevance. Hereby, a special focus was on the interaction of cell performance and cooling system. The simulation comprises battery models of commercial available 21700 cells as well as heat transfer models to highlight the influence of different cooling systems such as phase change materials for latent heat storage. The model allows to quickly assess different operating scenarios and main influencing parameters and thus, to develop new cool down and fast charging strategies adjusted to different cooling systems and areas of application. After high duty use phases, battery packs reach temperatures up to 70°C. To prevent accelerated aging due to high temperatures in the cells in the following charging step, the pack manufacturers have to ensure that the cells in the battery packs cool down to a certain temperature before charging. This cooling step significantly prolongs total charging times. Consequently, reducing these downtimes in between high duty use and charging as well as improving fast charging strategies (which fit the used cooling system) can significantly reduce the total charging time and ageing risk. These improvements are therefore beneficial for customer acceptance (usability) and long service lives (guarantee and maintenance risk for the manufacturer). The following use case was applied: The fully charged battery pack was discharged with 50A to zero SOC (step A, resembles e.g. working with an angle grinder). After it has cooled down to acceptable temperature (step B, cool down step), a charging step with 2C (8A, step C) followed. The performance of four different cooling systems were compared: (I) Non convective air (reference), (II) high heat transfer polymer, (III) latent heat storage materials (using phase change for cooling) and (III) cooling by air with forced convection (air cooling). The influence of different material parameters (e.g. thermal conductivity) as well as operation conditions (e.g. ambient temperature) were investigated. By reviewing different scenarios and applying a key performance indicator optimization, we can demonstrate that the total charging time can be reduced significantly. Compared to the reference scenario, shortening of up to 30 minutes was achieved in the investigated use case. Furthermore, the simulation study allows to highlight pros and cons of the different cooling systems.
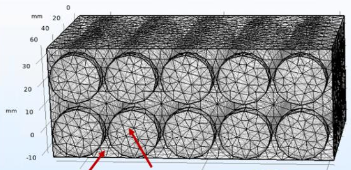
Download
- Veit Steinbauer, Volker Knoblauch, Power tool battery packs - shortening intervals of operation and charging by improved cooling strategy, Proceedings of the Comsol Conference Europe, Grenoble (2020).pdf - 0.45MB
- Veit Steinbauer, Power tool battery packs - shortening intervals of operation and charging by improved cooling strategy, Poster at the Comsol Conference 2020.pdf - 2MB