Structural Analysis on 3D Printed Objects Made from Experimentally Characterized Materials
Additive manufacturing (AM) is one of the most challenging technologies across a wide range of industrial fields and applications. When using a traditional manufacturing approach, the structural behaviour of a piece made from a homogeneous material is not affected by the mechanical processing method employed to create it. However, in additive manufacturing, the mechanical strength of a piece is highly dependent on the specific 3D printing process used to fabricate it.
The first purpose of this activity is to assess the different mechanical behaviours of specimens printed using various processing parameters, such as infill density and the number of outer layers. Then, the main goal is to develop numerical models that enable structural analyses of generic printed objects in COMSOL Multiphysics.
The adopted workflow for this activity consists of the following steps: printing specimens, conducting tensile stress-strain testing, modelling specimens, performing numerical-experimental validation of the models, and simulating the structure of selected printed objects. The entire workflow has been managed and developed at BE CAE & Test using the available hardware and software facilities.
The 3D model of the specimen is imported into the open-source slicing software Ultimaker Cura (Version 5.7.1). In Cura, the model is converted into a G-code file containing the instructions that the 3D printer follows to fabricate the object. The 3D printing technology used is Fused Deposition Modelling (FDM). The machine adopted for printing the specimens is the Creality CR-6 SE, and the material used is PLA. The print settings used are as follows: a layer height of 0.2 mm, a bed temperature of 60°C, and a nozzle temperature of 200°C. The adopted print speed is 50 mm/s. Mechanical characterization of the printed specimens is realised by using the tensile testing machine SHIMADZU AGS-X, assuring a maximum load of 10 kN for a speed range 0.001-1000 mm/min.
Modelling and simulations are performed using the Structural Mechanics Module of COMSOL Multiphysics v6.2. Because the stress-strain relationships are non-linear even at infinitesimal strains, the non-linear elastic material model is used. Additionally, due to the non-linearity at higher strains, the plasticity model is also employed, incorporating a specific hardening function. Once the validation procedure was successfully completed, a sample object was designed and printed according to a chosen set of printing parameters. This object was then both experimentally and numerically tested until failure. A very good agreement in structural behaviour was observed when comparing the numerical predictions to the experimental results.
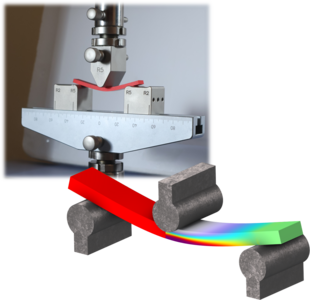
Download
- petrone-10801-poster.pdf - 2.04MB