Taking a Detailed Cross Section Out of a 3D Model to Increase Performance and Accuracy
Splitting a 3D model into two coupled components can increase performance [1]. Two offshore applications with the AC/DC module and the heat transfer module are presented, but the approach is general. The examples simulate the hotspot temperature in a three core cable with cross-sectional details such as thin metallic screens and armouring by small steel wires. In the first case, air-filled ducts with cables cross each other by a right angle in ground at different depths. The second example is a vertical cable in a J-tube in air. In both cases, the detailed cross section of the cable is unchanged along the cable length. Thus, it is possible to remove it and simulate the electromagnetic losses in a separate 2D model in Cartesian coordinates. It takes into account the phase shift of 120 degrees between the three AC current phases, skin effect in the conductors, eddy currents in the metallic screens and armouring, and the temperature coefficients of the metals. The full 3D models with cables need extremely fine mesh for acceptable results and simulate only heat losses, heat conduction and radiation. The first example has 400 million degrees of freedom and takes six hours. The split multi-physics model with normal mesh and air convection in the ducts calculates similar duct surface temperatures and in turn cable hot-spot temperature with 4 million degrees of freedom in 3 minutes. In the first application, removing the cable ducts leaves holes in the 3D ground, which considerably reduces the number of mesh elements. As the temperature can vary along the ducts, the 2D cross-section model of the cable in duct is surrounded by ground and the ambient temperature is varied by a parameter sweep. The sweep gives a relationship between the temperature on the duct outer surface and the resulting heat flux into the surrounding ground. This coupling function is linear and is set as inward heat flux surface boundary condition in the duct holes in the retained 3D ground model. In the J-tube example, 3D modeling is skipped completely. Whereas the first example simulates heat conduction in three-dimensional ground, the J-tube is reduced to a 2D vertical rectangle in rotational symmetry. As opposed to 3D, including natural convection of air in the J-tube turns out to work well in 2D, yielding more realistic results. The temperature and heat flux on the cable outer surface is directly coupled by probes between the 2D cable cross-section model and the 2D J-tube model, which are simulated together. Thus, a parameter sweep as intermediate step is not needed here. A similar solution for a twisted cable splits the cable itself into a 3D model of the metal parts for electromagnetic losses and a detailed 2D cross section for heat transfer, radiation and convection [2]. This is for one straight twisted cable, whereas our approach works for free routing of a constant cross section in a 3D environment.
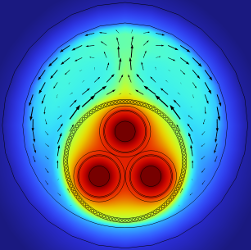
Download
- paper_krah.pdf - 0.97MB
- krah_9011_poster.pdf - 1.92MB
- 1_julius_krah.pdf - 0.65MB