Thermal-Elastohydrodynamic simulation of angular contact ball bearing using COMSOL Multiphysics®
Angular contact ball bearings (ACBB) are rolling bearings designed to support both axial and radial loads. The rolling elements (balls in this case) significantly decrease the power losses associated with rotating load bearing by replacing sliding with rolling. However, both the specific kinematic of ACBB and the depth of the ring grooves respectively generate spinning and sliding between the balls and the rings. Together, they contribute to generate frictional power losses. The specific kinematic of ACBB comes from the axial load the bearing is designed to withstand [1-2]: the rotation axes of the rings and the balls are not parallel to each other; this results in spinning induced sliding, and thus, frictional power losses. Moreover, the conformal elliptical contact between the rather deep grooves and the balls creates a large non planar contacting area. Such contact inherently involves sliding apart from the two pure rolling lines. Such sliding also contributes to frictional power losses. This study investigates the frictional power losses in ACBB by simulating the elliptical contact between a ball and a ring. Under motion, the lubricant fully separates the bodies in elastohydrodynamic lubrication condition. Because of the sliding, the lubricant is sheared which produces heat and activates non-Newtonian effects. An elastohydrodynamic model including both thermal and non-Newtonian effects [3] is used and the kinematic is defined accordingly to the application. Different simulations are run to predict the frictional power losses in the specific ACBB investigated.
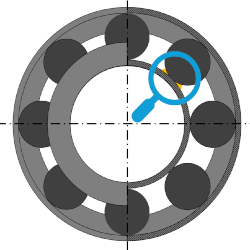
Download
- zhang_tehd_acbb_confcomsol_24_publication.pdf - 0.34MB
- wheeler_8691_poster.pdf - 1.1MB