Combining Elastoplastic and Creep Material Models
Application ID: 12397
This model shows how to combine different types of material nonlinearity, such as creep and elastoplasticity. In this specific example you will perform a stress and nonlinear strain analysis on a thick cylinder under a nonproportional loading: an initial temperature increase followed by a fluctuating pressure applied to the internal surface of the cylinder.
This load case involves two different nonlinear material behaviors: elastoplasticity and creep. The plastic behavior is introduced during the temperature increase and the rapid change of the pressure sign. The creep behavior develops under the constant pressure load applied to the pipe for a sufficiently long period of time.
The original model is a NAFEMS benchmark model described in Selected Benchmarks For Material Non-Linearity. The COMSOL Multiphysics solutions are compared with the reference data.
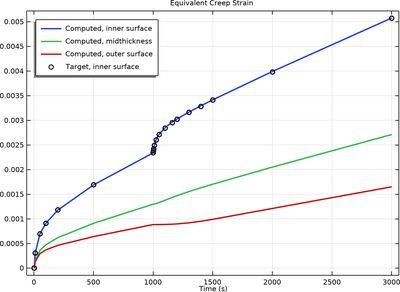
This model example illustrates applications of this type that would nominally be built using the following products:
however, additional products may be required to completely define and model it. Furthermore, this example may also be defined and modeled using components from the following product combinations:
- COMSOL Multiphysics® and
- Nonlinear Structural Materials Module and
- either the MEMS Module, or Structural Mechanics Module
The combination of COMSOL® products required to model your application depends on several factors and may include boundary conditions, material properties, physics interfaces, and part libraries. Particular functionality may be common to several products. To determine the right combination of products for your modeling needs, review the Tabella delle Funzionalità and make use of a free evaluation license. The COMSOL Sales and Support teams are available for answering any questions you may have regarding this.