Plate Heat Exchanger
Application ID: 252
The model has its emphasis on heat transport in a very small heat exchanger that is commonly used in the field of microelectromechanical systems (MEMS). In this case, it might be a reactive processes that needs heating.
The heat exchanger itself is constructed by stacking several pleated sheets or plates on top of each other while leaving a gap in between. The fluid used to transfer heat circulates in gaps between the corrugated walls.
To simplify the modeling, only a cross section between two plates is studied. The shape of the plates is, in this case, sinusoidal in order to increase the heat transfer area. The model is made more relevant by making the material properties, heat capacity, and viscosity functions of temperature — a true multiphysics model.
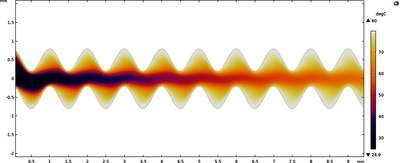
This model example illustrates applications of this type that would nominally be built using the following products:
however, additional products may be required to completely define and model it. Furthermore, this example may also be defined and modeled using components from the following product combinations:
- COMSOL Multiphysics® and
- either the Battery Design Module, CFD Module, Chemical Reaction Engineering Module, Corrosion Module, Electrochemistry Module, Electrodeposition Module, Fuel Cell & Electrolyzer Module, Heat Transfer Module, Microfluidics Module, Plasma Module, Polymer Flow Module, Porous Media Flow Module, or Subsurface Flow Module
The combination of COMSOL® products required to model your application depends on several factors and may include boundary conditions, material properties, physics interfaces, and part libraries. Particular functionality may be common to several products. To determine the right combination of products for your modeling needs, review the Tabella delle Funzionalità and make use of a free evaluation license. The COMSOL Sales and Support teams are available for answering any questions you may have regarding this.